Optimización de Energía –
Herramienta de Incremento de Valor
Por Victor Palomino y Ana Basauri
Introducción
En la industria, mejorar la eficiencia energética es clave para reducir costos y optimizar recursos. La Optimización de Energía (EO) permite un uso más inteligente de la energía, minimizando desperdicios y mejorando la rentabilidad.
A través de estrategias como la recuperación de calor y el análisis de Pinch, es posible identificar oportunidades para reutilizar la energía dentro de los procesos industriales. Su aplicación en sectores como la química, minería, alimentos y petróleo ha demostrado un impacto significativo en la reducción de costos operativos y el aumento de la eficiencia.
Este artículo explica qué es la EO, cómo se implementa y cuáles son sus beneficios en la industria.
¿Qué es la Optimización de Energía?
La Optimización de Energía es un conjunto de estrategias diseñadas para reducir el consumo energético y mejorar la eficiencia en procesos industriales. Su objetivo es encontrar el mejor equilibrio entre inversión inicial, costos operativos y rendimiento.
Para lograrlo, se analizan datos térmicos y de consumo energético, identificando oportunidades para recuperar y reutilizar calor. Esto se puede hacer a través de intercambiadores de calor o generadores de turbinas que convierten el calor residual en energía útil.
La Relación entre Energía y Calor
El calor y la energía están directamente relacionados. Durante años, las industrias han utilizado intercambiadores de calor en equipos como reactores y columnas de destilación para mejorar su eficiencia energética.
Desde la década de 1970, surgió un método más avanzado llamado integración energética, que optimiza el uso del calor en toda la planta en lugar de limitarse a equipos individuales. Este enfoque se basa en el análisis de Pinch, una técnica que permite reducir el consumo de energía al identificar las mejores oportunidades para reutilizar el calor dentro del proceso.
Beneficios del Análisis de Pinch
El análisis de Pinch ayuda a identificar fuentes y sumideros de calor dentro de un proceso industrial, permitiendo una integración eficiente de la energía. Sus principales beneficios incluyen:
- Reducción del consumo de energía.
- Disminución de costos operativos.
- Optimización del diseño del proceso.
- Mayor retorno de inversión (ROI).
¿Dónde se Aplica la Optimización de Energía?
La EO es clave en sectores que requieren grandes cantidades de energía, tales como:
- Petróleo y gas.
- Industria química y petroquímica.
- Minería y metalurgia.
- Papel y celulosa.
- Industria farmacéutica.
- Alimentos y bebidas.
Se estima que la EO se utiliza en el 30 % de los proyectos industriales a gran escala, con un aumento significativo en la refinación de petróleo.
¿En qué proyectos es aplicable la EO?
La EO puede aplicarse tanto en la construcción de nuevas plantas como en la optimización de procesos existentes. Sin embargo, no es aplicable en proyectos puramente eléctricos, mecánicos, de construcción o de control de sistemas.
Condiciones para Aplicar la EO
Para que la EO agregue valor a un proyecto, se deben cumplir ciertos criterios. Es importante realizar un análisis de Pinch en la etapa de planificación, documentar los hallazgos con diagramas y estudios de costos, identificar mejoras y aplicarlas en el diseño del proceso, y revisar los resultados con todas las áreas involucradas. En algunos casos, la implementación de la EO puede requerir una mayor inversión inicial, pero los ahorros en energía compensan estos costos a largo plazo.
¿Cómo se mide el éxito de la EO?
Para evaluar la efectividad de la EO, se analizan factores como la etapa del proyecto en la que se aplicó, el uso de un proceso estructurado y repetible, y las herramientas y software utilizados para su implementación.
Pasos para Implementar la Optimización de Energía
La EO se integra mejor en la fase de diseño del proceso. Su implementación sigue tres pasos fundamentales.
- El primero es el análisis del proceso, donde se determinan las temperaturas necesarias en cada etapa, se identifica cómo se usa el calor en la planta y se definen los flujos de materiales y sus restricciones operativas.
- El segundo paso es la evaluación de costos, que implica calcular el costo de los equipos de recuperación de calor, analizar el costo de la energía en el sitio y comparar diferentes alternativas de ahorro.
- Finalmente, en el diseño optimizado, se establecen los objetivos energéticos del proyecto, se ajusta el diseño del proceso para reducir el consumo de energía y se finalizan los diagramas de flujo optimizados.
Información Necesaria para un Estudio EO
Para realizar un estudio de EO, se requiere contar con diagramas de flujo del proceso, temperaturas clave de los procesos, datos sobre el consumo de energía, costos aproximados de equipos e información sobre el sistema de servicios públicos. En proyectos de modernización, también se deben considerar los datos de los equipos existentes para evaluar su rendimiento actual y determinar si es posible mejorar su eficiencia.
Herramientas VIP Complementarias
Aunque no existen otras prácticas similares a la EO, algunos métodos pueden complementarla. Las Clases de Calidad de Instalaciones (CFQ) ayudan a equilibrar costos de inversión y operación, mientras que el Modelado de Simulación de Confiabilidad (RSM) permite evaluar el impacto de la integración energética en la confiabilidad del sistema.
¿Quién Realiza el Estudio EO?
El estudio de EO es realizado por ingenieros de procesos, con el apoyo de especialistas en costos de capital, expertos en economía de proyectos y licenciadores de procesos
Duración de un Estudio EO
El tiempo requerido para realizar un estudio de EO varía según la complejidad del proyecto. Para una unidad de proceso, el análisis puede tomar aproximadamente un mes, mientras que para una planta completa, la optimización puede requerir varios meses debido a su complejidad.
Conclusión
La Optimización de Energía es una estrategia clave para mejorar la eficiencia, reducir costos y aumentar la rentabilidad en la industria. Su implementación permite un uso más inteligente de la energía, asegurando procesos más sostenibles y eficientes.
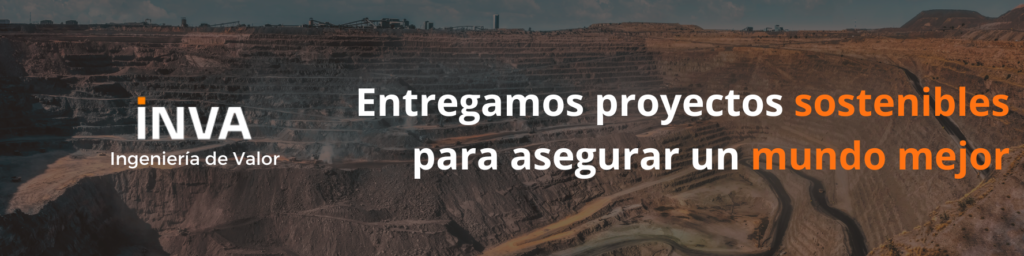